After nearly two years of planning and design, it’s time to swing some hammers.
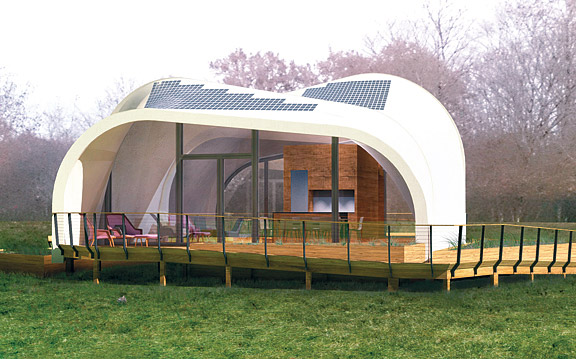
“If you just build a solar house, you’re not going to win,” says engineering student Isabelle Lubin ’16. “It’s about what you can do with it and how you can make a solar house different.”
Techstyle Haus will certainly be different. The outer shell of the 800-square-foot house will be made of Sheerfill, a flexible textile that’s often used on domed stadiums but has yet to be used on a house. The building will meet the standard for a passive house—using 90 percent less energy than a standard house—and will draw nearly all its power from a flexible solar array on the curved roof.
The team’s preliminary proposal was accepted into the competition in December 2012, and since then students have been refining their design and engineering the house’s key systems. Now it’s construction time. In a warehouse in Cranston, Rhode Island, students built the wooden platform on which the house will sit and the deck that will surround it. Then comes the mechanical core, along with the kitchen, the bathroom, and the electrical, heating, and ventilation systems. Once the project can move outside, the students will erect the house’s five steel structural ribs and attach the textile shell. Until then, the students are working in the shadow of two nineteen-foot-tall wooden mock-ups of the ribs, with which they are tweaking the assembly process for the exterior wall and finding the best way to attach insulation and the interior textile walls.
In addition to bringing together students from three different schools, the project has brought together companies that don’t often collaborate, says engineering student Gareth Rose ’16. “We’re doing things that have never been done before, [for example] trying to figure out how the fabric will meet the steel and the window frame at the same place,” he says. “One company is making the window frame and another is making the steel and another is making the textile. We try to have sponsor workshops where all the sponsors come and they get to talk to each other. It’s been fun watching them interact.”
If all goes as planned, the structure will be mostly assembled (minus the windows, which are being made in Europe) by April. After testing to make sure all the systems work, the house will be dismantled and packed into shipping containers. Then it’s off to Versailles, where the students have nine days to reassemble it.
Over the next few months, the team is in for some long hours, but they’re looking forward to it, Lubin says: “So far, it’s going great. It’s really exciting, especially as engineers, to finally be building something.”